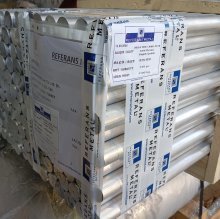
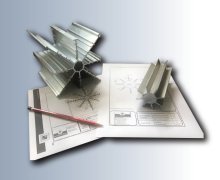
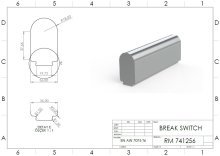
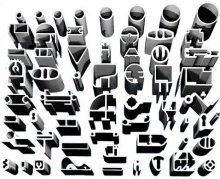
Plates
Sheets
Rod/Round Bar/Flat Bar
Tube/Extrusions/Profile
2024 clad
AMS QQ-A-250/5 / AlCu4Mg1 / 2024 clad / T3
Chemical Properties | % Value |
Silicon (Si) | 0,00 - 0,50 |
Chromium (Cr) | 0,00 - 0,10 |
Manganese (Mn) | 0,30 - 0,90 |
Magnesium (Mg) | 1,20 - 1,90 |
Copper (Cu) | 3,80 - 4,90 |
Titanium (Ti) | 0,00 - 0,20 |
Iron (Fe) | 0,00 - 0,50 |
Zinc (Zn) | 0,00 - 0,25 |
Aluminium (Al) | Balance |
Physical Properties | Value |
Density | 2.78 g/cm³ |
Melting Point | 502 °C |
Thermal Expansion | 22.9 µm/m°C |
Modulus of Elasticity | 73.1 GPa |
Thermal Conductivity | 121 W/m.K |
Electrical Resistivity | 30% IACS |
Mechanical Properties | Value |
Proof Strength | 310 MPa |
Yield Strength | 448 MPa |
Shear Strength | 276 MPa |
Elongation A50 mm | 15% |
Hardness | 120 HB |
Alclad 2024 T3 aluminum alloy is a material known for its high strength and excellent fatigue resistance, making it a preferred choice in the aerospace and aviation industries. The Alclad coating is a special version where a thin layer of pure aluminum is added to the core alloy, enhancing its corrosion resistance. The T3 temper indicates that the alloy has undergone solution heat treatment followed by natural aging, giving it high strength, machinability, and formability. These properties make Alclad 2024 T3 ideal for structural applications requiring high strength and durability.
This alloy is commonly used in critical aerospace components such as aircraft fuselages, wings, and landing gear. It is also favored in the automotive and defense industries. Due to its high fatigue resistance and lightweight properties, it is widely applied in equipment that carries heavy loads and operates under demanding conditions. Moreover, the alloy’s strength and machinability make it an exceptional choice for structural projects.
In terms of anodizing, Alclad 2024 T3 benefits from its pure aluminum coating, making it suitable for anodizing processes that enhance its corrosion resistance. However, the high copper content in the core alloy can impose limitations on the anodizing process. Regarding weldability, the copper content necessitates careful handling; specialized welding techniques and appropriate filler materials are recommended to minimize cracking risks and ensure reliable joints.
Although the bending and forming properties of Alclad 2024 T3 are good, the alloy’s high strength requires careful processing. This alloy is highly suitable for use in high-vibration environments due to its strength and elastic modulus, which provide excellent fatigue resistance. Its advantages include high strength, fatigue resistance, and lightweight characteristics, while its disadvantages are limited corrosion resistance and challenges in welding.
ALLOY DESIGNATIONS
Aluminium alloy Alclad 2024 T3 has similarities to the following standard designations and specifications:
As sheet: Alclad 2024 T3, AMS 4041, AMS QQ-A-250/5, AIR 9048-140, ASTM B209, BSL 109, WS 3.1364, EN 2090
Choosing Factors for 2024 clad T3
- Strength: Good
- Machining: Okay
- Weldability: Mediocre (Spot welding is the best choice)
- Formability: Low
- Corrosion Resistance: Poor
- Heat Treating: Yes
Some Well-Known Applications for 2024 clad T3
Aircraft floor beams,
Engine cowl skins,
It is also used in seat pans.
SUPPLIED FORMS
Alclad 2024 T3 is supplied in sheet.
- Sheet