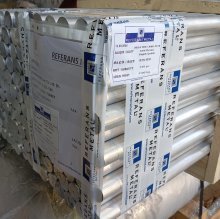
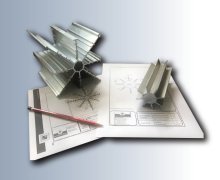
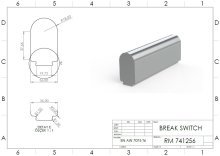
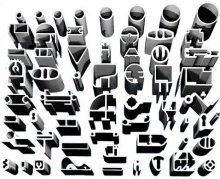
Cold Drawn Round Bar
Cold Drawn Tube
2024
Cold Drawn/Finished (CF) / AlCu4Mg1 (Soğuk Çekim) / 2024 / O
Chemical Properties | % Value |
Silicon (Si) | 0,00 - 0,50 |
Chromium (Cr) | 0,00 - 0,10 |
Manganese (Mn) | 0,30 - 0,90 |
Magnesium (Mg) | 1,20 - 1,80 |
Copper (Cu) | 3,80 - 4,90 |
Titanium (Ti) | 0,00 - 0,15 |
Iron (Fe) | 0,00 - 0,50 |
Zinc (Zn) | 0,00 - 0,25 |
Aluminium (Al) | Balance |
Titanium + Zirconium (Ti+Zr) | 0,00 - 0,20 |
Physical Properties | Value |
Density | 2.78 g/cm³ |
Melting Point | 502 °C |
Thermal Expansion | 23.2 µm/m-°C |
Modulus of Elasticity | 73.1 GPa |
Thermal Conductivity | 193 W/m.K |
Electrical Resistivity | 30% IACS |
Mechanical Properties | Value |
Proof Strength | 100 MPa |
Yield Strength | 210 MPa |
Shear Strength | 130 MPa |
Elongation A50 mm | 15% |
Hardness | 47 HB |
The cold-drawn 2024 O aluminum alloy is known for its high strength and good machinability. Belonging to the aluminum-copper alloy class, it is ideal for demanding engineering applications due to its lightweight and high strength. It is commonly used in industries such as automotive, aerospace, and space, especially for structural components requiring high performance. The cold-drawing process ensures a homogeneous microstructure, enhancing the alloy's mechanical properties.
The 2024 O alloy has limited suitability for anodizing. Its high copper content may hinder the formation of a strong oxide layer, making anodizing less effective. As a result, alternative protective coatings are often used. In terms of weldability, the alloy also presents challenges. The high copper content increases the risk of cracking in the weld area, requiring special welding techniques and appropriate filler materials to overcome these difficulties.
In terms of formability, the 2024 O alloy is quite machinable. Despite its high strength, it can be easily bent and shaped using the right processing techniques. The cold-drawing process allows for better formability. The alloy is also suitable for use in high-vibration environments, as its high strength and elastic modulus make it resistant to vibrations, making it a reliable choice for automotive and aerospace applications.
Regarding corrosion resistance, the 2024 O alloy has lower resistance compared to other aluminum alloys due to its copper content. This can limit its use in marine and humid environments. However, this limitation can be overcome with appropriate coatings and protective measures. The alloy's advantages include high strength, good machinability, and light weight, while its drawbacks include challenges with welding, limited anodizing capabilities, and lower corrosion resistance.
ALLOY DESIGNATIONS
Aluminium alloy 2024 O has similarities to the following standard designations and specifications:
As Plate and Sheet: 2024 O, AMS QQ-A-250/4, AMS 4035, AIR 9048-100, WS 3.1359, ASTM B209
As Alclad Sheet: 2024 O, AMS QQ-A-250/5, AMS 4040, AIR 9048-130, BS L 110, WS 3.1364, ASTM B209
As Cold Drawn Round Bar: 2024 O, WW-T-700/3, AMS 4087
Choosing Factors for 2024 O
- Strength: High
- Machining: Okay
- Weldability: Moderate (Spot welding is the best choice)
- Formability: Weak
- Corrosion Resistance: Low
- Heat Treating: Yes
Some Well-Known Applications for 2024 O
Leading edge skins of aircraft wings,
Components of landing gears,
It is also used in interior fuselage brackets.
SUPPLIED FORMS
2024 O aluminum alloy is supplied in plate, sheet, bar/round bar, tube/extrusion.
- Plate
- Sheet
- Round Bar / Bar
- Tube / Extrusion
Mechanical Properties | |||
Thickness (mm) | Proof Strength (Min.) | Yield Strength (Min.) | Elongation A50 mm % |
0,5 mm | 109,6 MPa | 193 MPa | 12% |
1,5 mm | 105 MPa | 185 MPa | 20% |
2,0 mm | 110 MPa | 196 MPa | 20% |