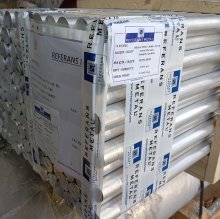
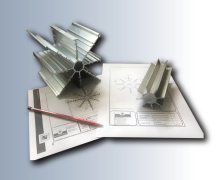
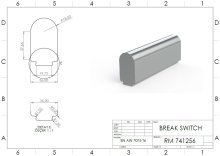
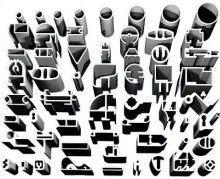
Platos
Hojas
Barras Circulares
Tubos / Extrusion / Perfil
2124
AMS 4221 / AlCu4Mg1 / 2124 / T8151
Chemical Properties | % Value |
Silicon (Si) | 0,00 - 0,20 |
Chromium (Cr) | 0,00 - 0,10 |
Manganese (Mn) | 0,30 - 0,90 |
Magnesium (Mg) | 1,20 - 1,80 |
Copper (Cu) | 3,80 - 4,90 |
Titanium (Ti) | 0,00 - 0,15 |
Iron (Fe) | 0,00 - 0,30 |
Zinc (Zn) | 0,00 - 0,25 |
Aluminium (Al) | Balance |
Physical Properties | Value |
Density | 2.78 g/cm³ |
Melting Point | 502 °C |
Thermal Expansion | 21.1 µm/m-°C |
Modulus of Elasticity | 71 GPa |
Thermal Conductivity | 151 W/m.K |
Electrical Resistivity | 38% IACS |
Mechanical Properties | Value |
Proof Strength | 430 MPa |
Yield Strength | 490 MPa |
Shear Strength | 280 MPa |
Elongation A50 mm | 5.7% |
Hardness | 128 HB |
The 2124 T8151 aluminum alloy is known for its high strength and excellent durability. As part of the aluminum-copper alloy class, this material is primarily used in applications that require high performance, such as aerospace, space, and military industries. The T8151 temper is produced through a specialized heat treatment process to enhance the alloy's strength and durability. Its high strength and light weight make it ideal for use in structural components that need to perform under demanding conditions.
The 2124 T8151 alloy is not suitable for anodizing. Due to its high copper content, anodizing does not form a strong oxide layer on the surface. This makes anodizing an ineffective method for protection, and alternative coating techniques are typically used. In terms of weldability, the 2124 T8151 aluminum alloy presents challenges. The high copper content increases the risk of cracking in the weld area, so special welding techniques and appropriate filler materials are necessary to minimize this risk.
In terms of bending and forming, the 2124 T8151 alloy requires careful processing due to its high strength. However, with the proper techniques, successful bending and shaping operations can be achieved. Additionally, this alloy is suitable for use in high-vibration environments. Its high durability and elastic modulus make it ideal for components subjected to vibrations, such as engine parts, aircraft structural components, and other components exposed to high-stress environments.
Regarding corrosion resistance, the 2124 T8151 aluminum alloy has limited resistance due to its high copper content. This can limit its use in harsh environments, such as marine and humid conditions. However, these limitations can be overcome with proper coating methods and surface treatments, improving the alloy's corrosion resistance. The advantages of the 2124 T8151 alloy include high strength, good machinability, and light weight, while its drawbacks include lower corrosion resistance and welding challenges.
ALLOY DESIGNATIONS
Aluminium alloy 2124 T8151 has similarities to the following standard designations and specifications:
Plates per: ASTM B211, AMS QQ-A-225/6, AMS 4339
Choosing Factors for 2124 T8151
- Strength: Medium
- Machining: Good
- Weldability: Good (Spot welding is the best choice)
- Formability: Weak
- Corrosion Resistance: Low
- Heat Treating: Yes
Some Well-Known Applications for 2124 T8151
Engine support structures of aircrafts,
In parts requiring short transverse ductility,
It is also used in fuselage bulkheads.
SUPPLIED FORMS
2124 T8151 is supplied in the plate form.
- Plate
Mechanical Properties | |||
Thickness (mm) | Proof Strength (Min.) | Yield Strength (Min.) | Elongation A50 mm % |
Over 38.1 up to & incl. 50.8 | 393 MPa | 455 MPa | %5 |
Over 50,8 up to & incl. 76,2 | 393 MPa | 448 MPa | %4 |
Over 76,2 up to & incl. 101,6 | 386 MPa | 448 MPa | %4 |
Over 101,6 up to & incl. 127 | 379 MPa | 441 MPa | %4 |
Over 127 up to & incl. 152,4 | 372 MPa | 434 MPa | %4 |