
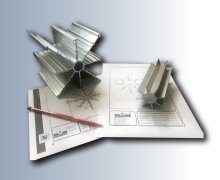
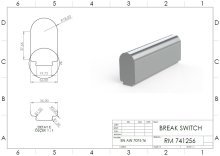
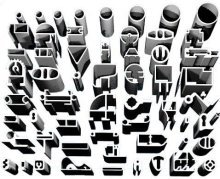
Dalle
Tôle
Barre ronde
Tube/ Extrusion/ Profil
2219 clad
AMS 4094 / AlCu6Mn / 2219 clad / T851
Chemical Properties | % Value |
Silicon (Si) | 0,00 - 0,20 |
Manganese (Mn) | 0,20 - 0,40 |
Magnesium (Mg) | 0,00 - 0,02 |
Copper (Cu) | 5,80 - 6,80 |
Titanium (Ti) | 0,02 - 0,10 |
Iron (Fe) | 0,00 - 0,30 |
Zinc (Zn) | 0,00 - 0,10 |
Nickel (Ni) | 0,00 - 0,20 |
Aluminium (Al) | Balance |
Titanium + Zirconium (Ti+Zr) | 0,10 - 0,25 |
Physical Properties | Value |
Density | 2.84 g/cm³ |
Melting Point | 543 °C |
Thermal Expansion | 20.8 µm/m-°C |
Modulus of Elasticity | 74 GPa |
Thermal Conductivity | 120 W/m.K |
Electrical Resistivity | 30% IACS |
Mechanical Properties | Value |
Proof Strength | 290 MPa |
Yield Strength | 400 MPa |
Shear Strength | 210 MPa |
Elongation A50 mm | 8.0 % |
Hardness | 130 HB |
Alclad 2219 T851 aluminum alloy is renowned for its high strength, excellent thermal stability, and good weldability. The Alclad version features a thin layer of pure aluminum on the surface, enhancing its corrosion resistance. The T851 temper indicates that the alloy has undergone solution heat treatment, stress relieving, and artificial aging processes, providing it with superior durability and fatigue resistance. These characteristics make Alclad 2219 T851 an ideal material for applications in aerospace, space exploration, and military projects where strength and durability are critical.
In terms of anodizing, Alclad 2219 T851 aluminum alloy is compatible with anodizing processes thanks to its pure aluminum coating. However, the high copper content in the core alloy can limit the effectiveness of anodizing for long-term corrosion protection. Additional coating techniques or surface treatments are often used to enhance durability in harsh environments. The alloy also excels in weldability, producing strong and reliable joints when proper filler materials and welding techniques are employed. This makes it an excellent choice for structural applications where integrity is paramount.
For forming and bending, Alclad 2219 T851 requires careful handling due to its high strength. Nonetheless, it can be successfully bent and shaped using appropriate methods, making it suitable for complex designs. Its excellent fatigue resistance and ability to withstand dynamic loads make it particularly well-suited for use in high-vibration environments. These properties make it ideal for aircraft structures, engine components, and other critical parts exposed to mechanical loads and vibrations.
The corrosion resistance of Alclad 2219 T851 is enhanced by the Alclad coating, though the copper content in the core alloy somewhat limits its natural corrosion resistance. Additional surface treatments may be necessary for use in extreme environments. The advantages of Alclad 2219 T851 include high strength, good weldability, fatigue resistance, and enhanced corrosion resistance, while its disadvantages include the need for careful handling during forming and limited natural corrosion resistance. These features make it an excellent material for projects requiring thermal durability and structural integrity.
As Alclad sheet; 2219 T851 clad, ASTM B209, UNS A92219, AMS 4094, ISO AlCu6Mn
Choosing Factors for 2219 T851 clad
- Strength: Perfect
- Machining: Weak
- Weldability: Very good
- Formability: Okay
- Corrosion Resistance: Significant
- Heat Treating: Yes
Some Well-Known Applications for 2219 T851 clad
In aircraft landing gear in the aerospace industry,
As a component of bicycle frames and bridges,
It has many uses, including in the engine frames of rockets.
- Sheet