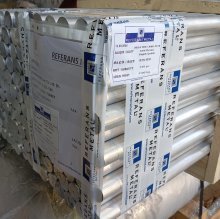
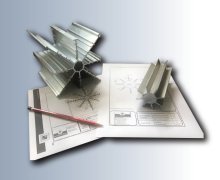
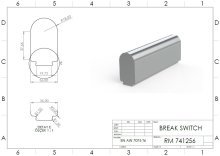
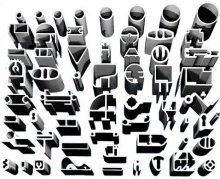
Plates
Sheets
Rod/Round Bar/Flat Bar
Tube/Extrusions/Profile
2618A
AIR 9048.640 / AlCu2Mg1.5Ni / 2618A / T851
Chemical Properties | % Value |
Silicon (Si) | 0,00 - 0,25 |
Tin (Sn) | 0,00 - 0,05 |
Manganese (Mn) | 0,00 - 0,20 |
Magnesium (Mg) | 1,20 - 1,80 |
Copper (Cu) | 1,20 - 1,80 |
Lead (Pb) | 0,00 - 0,05 |
Titanium (Ti) | 0,00 - 0,20 |
Iron (Fe) | 0,90 - 1,40 |
Zinc (Zn) | 0,00 - 0,15 |
Nickel (Ni) | 0,80 - 1,40 |
Aluminium (Al) | Balance |
Physical Properties | Value |
Density | 2.77 g/cm³ |
Melting Point | 549 °C |
Thermal Expansion | 22.3 µm/m.°C |
Modulus of Elasticity | 72 GPa |
Thermal Conductivity | 147 W/m.K |
Electrical Resistivity | 37% IACS |
Mechanical Properties | Value |
Proof Strength | 410 MPa |
Yield Strength | 440 MPa |
Shear Strength | 260 MPa |
Elongation A50 mm | % 4.5 |
Hardness | 134 - 135 HB |
The 2618A T851 aluminum alloy is known for its high-temperature strength, excellent mechanical properties, and lightweight nature. As part of the aluminum-copper alloy class, it is particularly preferred for applications requiring high strength and thermal resistance. The T851 temper, achieved through a specific heat treatment process, provides the alloy with high durability, stress resistance, and the ability to perform well at elevated temperatures. These characteristics make the 2618A T851 alloy commonly used in structural components for demanding industries such as aerospace, space, and defense.
In terms of anodizing, the 2618A T851 alloy has limited suitability. Due to its high copper content, anodizing may not form an effective oxide layer, which may lead to the use of alternative coating methods for protection instead of anodizing. For weldability, the 2618A T851 aluminum alloy requires a careful welding process due to its high copper content and other alloying elements. The risk of cracking during welding is increased, so special welding techniques and appropriate filler materials are necessary to minimize this risk.
Regarding bending and forming, the 2618A T851 aluminum alloy, despite its high strength, can be successfully shaped with the right processing techniques. This makes it suitable for applications that require both high durability and the ability to form complex shapes, such as engine parts and structural components. Additionally, it is suitable for use in high-vibration environments. Its high elastic modulus and durability make it ideal for components exposed to vibrations in industries like aerospace and automotive.
In terms of corrosion resistance, the 2618A T851 aluminum alloy has limited resistance due to its high copper content. This can restrict its use in harsh environments, such as marine and humid conditions. However, these limitations can be overcome with appropriate surface coatings and protective treatments, enhancing the alloy's corrosion resistance. The advantages of the 2618A T851 alloy include high-temperature resistance, excellent mechanical properties, and lightweight nature, while its disadvantages include lower corrosion resistance and welding challenges.
As Plate; 2618A T851, ASTM B209, UNS A92618, AIR 9048.640, ISO AlCu2Mg1.5Ni, WNR 3.1924, EN 2123
Choosing Factors for 2618A T851
- Strength: High
- Machining: Good
- Weldability: Poor
- Formability: Good
- Corrosion Resistance: Average
- Heat Treating: Yes
Some Well-Known Applications for 2618A T851
Mainly in the aerospace sector,
In aerospace parts and as a structural component of engines,
It has many uses, including parts in the high-tech industry.
- Plate
Mechanical Properties | |||
Thickness (mm) | Proof Strength (Min.) | Yield Strength (Min.) | Elongation A50 mm % |
Up to & incl. 10 | Min 320 MPa | Min 400 MPa | %5 |
Up to & incl. 10 | Min 340 MPa | Min 420 MPa | %5 |