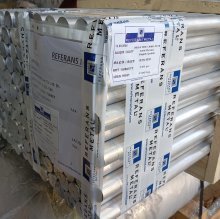
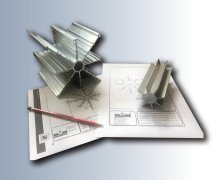
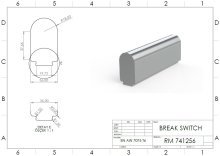
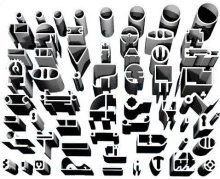
Калиброванные прутки
Трубы волоченые
2014
Cold Drawn/Finished (CF) / AlCu4SiMg (Soğuk Çekim) / 2014 / T4510
Chemical Properties | % Value |
Silicon (Si) | 0,50 - 1,20 |
Tin (Sn) | 0,0 - 0,15 |
Chromium (Cr) | 0,00 - 0,10 |
Manganese (Mn) | 0,40 - 1,20 |
Magnesium (Mg) | 0,20 - 0,80 |
Copper (Cu) | 3,90 - 5,00 |
Titanium (Ti) | 0,00 - 0,15 |
Iron (Fe) | 0,00 - 0,70 |
Zinc (Zn) | 0,00 - 0,25 |
Aluminium (Al) | Balance |
Physical Properties | Value |
Density | 2.80 g/cm³ |
Melting Point | 507 °C |
Thermal Expansion | 22.5 µm/m.°C |
Modulus of Elasticity | 73 GPa |
Thermal Conductivity | 150 W/m.K |
Electrical Resistivity | %40 IACS |
Mechanical Properties | Value |
Proof Strength | 280 MPa |
Yield Strength | 410 MPa |
Shear Strength | 240 MPa |
Elongation A50 mm | %11 |
Hardness | 102 HB |
The cold-drawn 2014 T4510 aluminum alloy is known for its high strength, good machinability, and durability. It belongs to the aluminum-copper alloy class, making it ideal for structural and mechanical applications. The alloy is commonly used in industries such as automotive, aerospace, and military, where high-performance materials are required.
The 2014 T4510 alloy is not suitable for anodizing. Due to its high copper content, anodizing is less effective at creating a protective oxide layer, and alternative protective coatings are often used instead.
In terms of weldability, the 2014 T4510 alloy presents challenges. The high copper content increases the risk of cracking in the weld zone, so special welding techniques and filler materials must be used. However, with the correct approach, strong and durable welds can be achieved.
The alloy offers good formability for bending and shaping, but due to its high strength, care must be taken during these processes. With the proper methods, successful bending can be achieved without compromising the material's integrity.
The 2014 T4510 aluminum alloy can be used in high-vibration environments due to its high strength and elastic modulus. This makes it suitable for applications in automotive and aerospace industries, particularly in engine and chassis components, where vibration resistance is crucial.
Corrosion resistance is a drawback of this alloy, as its high copper content makes it more prone to corrosion compared to other aluminum alloys. This may limit its use in marine environments or other areas exposed to moisture and salt. However, corrosion resistance can be improved with appropriate coatings and protective treatments.
The advantages of the 2014 T4510 aluminum alloy include high strength, good machinability, vibration resistance, and lightweight properties. Its disadvantages include limited anodizing suitability, welding challenges, and lower corrosion resistance, particularly in harsh environments. Overall, the 2014 T4510 alloy is ideal for applications requiring high strength, but attention should be paid to its corrosion resistance and welding requirements.
As Extruded Round/Flat Bar, Tube; 2014 T4510, ASTM B221, UNS A92014, EN 2634, WNR 3.1255, MIL-A-21180, ISO AlCu4SiMg
As Cold Drawn Tube: 2014 T4510, ASTM B211, UNS A92014, ASTM B928, WNR 3.1255, MIL-A-21180, ISO AlCu4SiMg
Choosing Factors for 2014 T4510
- Strength: Great
- Machining: Great
- Weldability: Bad
- Formability: Okay
- Corrosion Resistance: Weak
- Heat Treating: Yes
Some Well-Known Applications for 2014 T4510
In the automotive industry and bridge construction,
As a military vehicle and high-strength building material,
It is mainly used in the aerospace industry.
- Rod / Round Bar / Flat Bar
- Tube/Profile