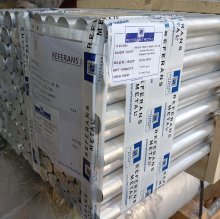
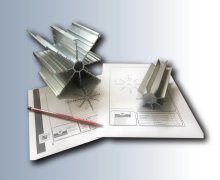
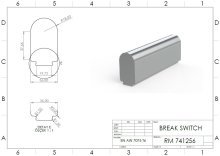
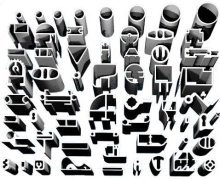
冷拔 铝圆棒
冷拔 圆管
2017A
Cold Drawn/Finished (CF) / AlCu4MgSi(A) (Soğuk Çekim) / 2017A / T3510
化学性质 | % 值 |
Silicon (Si) | 0,20 - 0,80 |
Chromium (Cr) | 0,00 - 0,10 |
Manganese (Mn) | 0,40 - 1,0 |
Magnesium (Mg) | 0,40 - 1,00 |
Copper (Cu) | 3,50 - 4,50 |
Titanium (Ti) | 0,00 - 0,25 |
Iron (Fe) | 0,00 - 0,70 |
Zinc (Zn) | 0,00 - 0,25 |
Aluminium (Al) | Balance |
物理特性 | 值 |
Density | 2.79 g/cm³ |
Melting Point | 510 °C |
Thermal Expansion | 22.9 µm/m°C |
Modulus of Elasticity | 72 GPa |
Thermal Conductivity | 150 W/m.K |
Electrical Resistivity | 34 % IACS |
机械性能 | 值 |
Proof Strength | 280 MPa |
Yield Strength | 460 MPa |
Shear Strength | 270 MPa |
Elongation A50 mm | 10% |
Hardness | 95 HB |
The cold-drawn 2017A T3510 aluminum alloy is known for its high strength and good machinability. Belonging to the aluminum-copper alloy class, it is particularly used in demanding mechanical and structural applications. In addition to its high strength, its lightweight nature is a significant advantage. These properties make it a popular choice in industries such as automotive, aerospace, and defense. The alloy is suitable for structural components that require durability and strength, making it widely used in many industrial sectors.
The 2017A T3510 alloy has low suitability for anodizing. Due to its high copper content, anodizing has limited effectiveness on this alloy, making it difficult to form a protective oxide layer. Therefore, alternative coating methods are used to protect the surface of the material. In terms of weldability, the high copper content also increases the risk of cracking during welding. Special welding techniques should be employed to achieve strong, reliable welds. With proper precautions, high-quality welds can be achieved.
This alloy offers good formability for bending and shaping. The cold-drawing process provides a homogeneous microstructure, making it easier to work with. Despite its high strength, successful bending can be performed using the right processing techniques. Additionally, the 2017A T3510 alloy is suitable for high-vibration environments. Its durable structure makes it ideal for automotive, aerospace, and other industries where components are subjected to high levels of stress and vibration. This feature provides significant advantages in components such as engine parts and chassis.
In terms of corrosion resistance, the 2017A T3510 alloy has some limitations due to its copper content. This makes it less suitable for marine environments or applications exposed to moisture and salt. However, proper coating and surface treatments can improve its corrosion resistance. While the alloy offers high strength, machinability, and light weight, it may face challenges related to welding and corrosion resistance. With the correct processing and protective measures, these drawbacks can be minimized, making the alloy a reliable choice for various industrial applications.
As Cold Drawn Tube, Profile: 2017A T3510, AMS QQ-A-225/5, ASTM B210, UNS A92017A, WNR 3.1325, DIN AlCuMg1, ASTM B565, ASTM B316, ISO AlCu4MgSi (A)
Choosing Factors for 2017A T3510
- Strength: Excellent
- Machining: Great
- Weldability: Mediocre
- Formability: Good
- Corrosion Resistance: Fair
- Heat Treating: Yes
Some Well-Known Applications for 2017A T3510
As a component of clothing hangers, fasteners,
From the aerospace industry to crochet and knitting needles,
It has many areas of use, including the transportation sector and the automotive industry.
- Tube/Profile
机械性能 | |||
厚度 (mm) | 证明力量 (Min.) | 屈服强度 (Min.) | Uzama % |
Over 25 up to & incl. 75 | 270 MPa | 400 MPa | %10 |
Over 75 up to & incl. 150 | 260 MPa | 390 MPa | %9 |
Over 150 up to & incl. 200 | 240 MPa | 370 MPa | %8 |
Over 200 up to & incl. 250 | 220 MPa | 360 MPa | %7 |