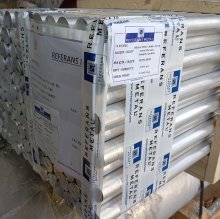
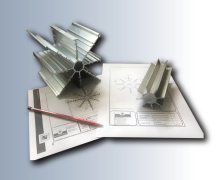
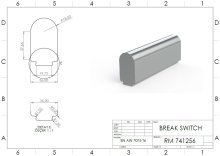
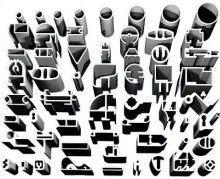
Barras Estiradas en Frío
Tubos Estirados en Frío
2014
Cold Drawn/Finished (CF) / AlCu4PbMgMn (Soğuk Çekim) / 2014 / T6510
Chemical Properties | % Value |
Silicon (Si) | 0,50 - 0,90 |
Chromium (Cr) | 0,00 - 0,10 |
Manganese (Mn) | 0,40 - 1,20 |
Magnesium (Mg) | 0,20 - 0,80 |
Copper (Cu) | 3,90 - 5,00 |
Titanium (Ti) | 0,00 - 0,15 |
Iron (Fe) | 0,00 - 0,50 |
Zinc (Zn) | 0,00 - 0,25 |
Nickel (Ni) | 0,00 - 0,10 |
Aluminium (Al) | Balance |
Physical Properties | Value |
Density | 2.80 g/cm³ |
Melting Point | 640 °C |
Thermal Expansion | 22.8 x 10^-6 /K |
Modulus of Elasticity | 73 GPa |
Thermal Conductivity | 155 W/m.K |
Electrical Resistivity | %40 IACS |
Mechanical Properties | Value |
Proof Strength | 430 MPa |
Yield Strength | 510 MPa |
Shear Strength | 280 MPa |
Elongation A50 mm | 6% |
Hardness | 135 HB |
The 2014 T6510 alloy provides excellent strength and hardness, making it ideal for structural components that bear heavy loads. The cold-drawing process results in a homogeneous microstructure, enhancing mechanical properties and offering excellent machinability. Additionally, the alloy’s lightweight nature provides advantages in terms of handling and assembly.
The 2014 T6510 alloy is not suitable for anodizing. Due to its high copper content, anodizing is less effective in creating a protective oxide layer. Therefore, alternative protective coatings are typically used to safeguard the material.
In terms of weldability, the 2014 T6510 alloy presents challenges due to its high copper content, which increases the risk of cracking during welding. Special welding techniques and appropriate filler materials are required to achieve strong and durable welds. However, with the right approach, high-quality welds can be made, although careful attention is needed during the welding process.
The alloy offers good formability for bending, but its high strength requires careful handling. While the alloy is harder than many others, successful bending can still be achieved with the proper processing techniques.
When it comes to corrosion resistance, the 2014 T6510 alloy shows limited resistance due to its high copper content. This can restrict its use in marine environments or other applications exposed to moisture and salt. However, corrosion resistance can be enhanced with the application of appropriate protective coatings and surface treatments.
The advantages of the 2014 T6510 aluminum alloy include its high mechanical strength and hardness, good machinability, vibration resistance, and lightweight properties. On the other hand, its disadvantages include limited anodizing suitability, challenges with weldability (due to the risk of cracking), and lower corrosion resistance, especially in marine or humid environments.
Overall, the 2014 T6510 aluminum alloy is an excellent choice for applications requiring high strength. However, attention should be paid to potential issues with anodizing, welding, and corrosion resistance, which can be mitigated through proper processing and protective measures.
Cold Drawn Tubes per; 2014 T6510, AMS 4121, ASTM B211, UNS A92014, ASTM B928, BS L 168, WNR 3.1255, ISO AlCu4SiMg
Extruded Round Bars and Tubes per: 2014 T6510, ASTM B210, UNS A92014, EN 2635, WNR 3.1255, ISO AlCu4SiMg,
Choosing Factors for 2014 T6510
- Strength: Great
- Machining: Very good
- Weldability: Poor
- Formability: Good
- Corrosion Resistance: Weak
- Heat Treating: Yes
Some Well-Known Applications for 2014 T6510
In places where weapons production and high-durability materials are required,
In the defense industry and as armored component,
It is also used mainly in the aerospace industry.
- Rod / Round Bar / Flat Bar
- Tube/Profile
Mechanical Properties | |||
Thickness (mm) | Proof Strength (Min.) | Yield Strength (Min.) | Elongation A50 mm % |
Up to & incl 2.5 | 370 MPa | 415 MPa | %6 |
Over 2.5 up to and incl. 10 | 385 MPa | 435 MPa | %6 |
Over 10 up to and incl. 25 | 415 MPa | 460 MPa | %7 |
Over 75 up to and incl. 100 | 435 MPa | 480 MPa | %7 |
Over 100 up to and incl. 150 | 420 MPa | 465 MPa | %7 |
Over 150 up to and incl. 200 | 390 MPa | 435 MPa | %7 |