
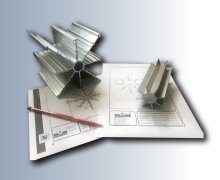
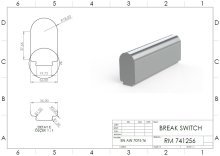
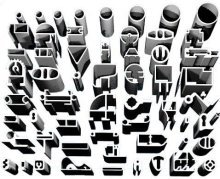
Dalle
Tôle
Barre ronde
Tube/ Extrusion/ Profil
7010
AMS 4204 / AlZn6MgCu / 7010 / T7651
Chemical Properties | % Value |
Silicon (Si) | 0,00 - 0,12 |
Chromium (Cr) | 0,00 - 0,05 |
Manganese (Mn) | 0,00 - 0,10 |
Magnesium (Mg) | 2,10 - 2,60 |
Copper (Cu) | 1,50 - 2,00 |
Titanium (Ti) | 0,00 - 0,06 |
Iron (Fe) | 0,00 - 0,15 |
Zinc (Zn) | 5,70 - 6,70 |
Aluminium (Al) | Balance |
Titanium + Zirconium (Ti+Zr) | 0,10 - 0,16 |
Physical Properties | Value |
Density | 2.82 g/cm³ |
Melting Point | 475 °C |
Thermal Expansion | 23,7 µm/m.°C |
Modulus of Elasticity | 70 GPa |
Thermal Conductivity | 150 W/m.K |
Electrical Resistivity | 40% IACS |
Mechanical Properties | Value |
Proof Strength | 500 MPa |
Yield Strength | 570 MPa |
Shear Strength | 330 MPa |
Elongation A50 mm | %6 |
Hardness | 83 HB |
The 7010 T7651 aluminum alloy is known for its high strength, durability, and excellent mechanical properties. As part of the aluminum-zinc alloy family, it is primarily used in aerospace, space, and high-performance structural applications. The T7651 temper, achieved through specific heat treatments, provides the alloy with high durability, stress resistance, and hardness while maintaining its machinability. These characteristics make the 7010 T7651 alloy ideal for heavy-load-bearing components used in demanding environments.
The 7010 T7651 aluminum alloy has limited suitability for anodizing. Its high zinc content prevents the formation of an effective oxide layer during anodizing, making anodizing an unsuitable method for protection. As a result, other coating methods are typically used to protect the alloy. In terms of weldability, the 7010 T7651 alloy requires careful handling during welding. The high zinc content increases the risk of cracking during welding, so special welding techniques and filler materials must be used to minimize this risk.
In terms of bending and forming, the 7010 T7651 aluminum alloy presents challenges due to its high strength. However, with the correct processing techniques, successful bending and forming can be achieved. Additionally, the 7010 T7651 alloy is suitable for use in high-vibration environments. Its high elastic modulus and durability make it ideal for components in automotive and aerospace industries, such as engine parts, chassis, and other vibration-resistant components.
Regarding corrosion resistance, the 7010 T7651 aluminum alloy may exhibit limited resistance compared to other aluminum alloys due to its high zinc content. However, its corrosion resistance can be improved with proper coatings and surface treatments. The advantages of the 7010 T7651 alloy include high strength, durability, and lightweight properties, while its disadvantages include limited corrosion resistance and challenges in welding.
Choosing Factors for 7010 T7651
- Strength: Exquisite
- Machining: Okay
- Weldability: Poor
- Formability: Weak
- Corrosion Resistance: Excellent
- Heat Treating: Yes
Some Well-Known Applications for 7010 T7651
It is used in mold and model making,
In airplane bodies,
In structural parts of airplane wings.
- Plate