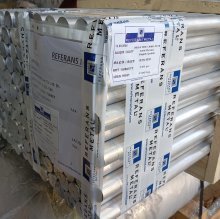
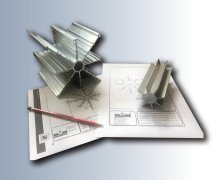
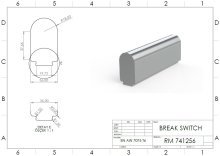
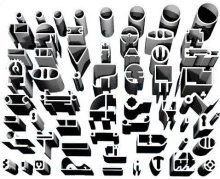
Листы/Плиты
Лист
Бар/Листовая Сталь
Трубы/Профили
2014 clad
AIR 9048.080 / AlCu4SiMg / 2014 clad / T62
Chemical Properties | % Value |
Silicon (Si) | 0,5 - 1,2 |
Chromium (Cr) | 0,00 - 0,10 |
Manganese (Mn) | 0,40 - 1,20 |
Magnesium (Mg) | 0,20 - 0,80 |
Copper (Cu) | 3,90 - 5,00 |
Titanium (Ti) | 0,00 - 0,15 / 0,00 - 0,20 |
Iron (Fe) | 0,00 - 0,7 |
Zinc (Zn) | 0,00 - 0,25 |
Aluminium (Al) | Balance |
Physical Properties | Value |
Density | 2.8 g/cm³ |
Melting Point | 507 °C |
Thermal Expansion | 22.7 µm/m°C |
Modulus of Elasticity | 72 GPa |
Thermal Conductivity | 130 W/m.K |
Electrical Resistivity | 40 % IACS |
Mechanical Properties | Value |
Proof Strength | 440 MPa |
Yield Strength | 500 MPa |
Shear Strength | 290 MPa |
Elongation A50 mm | 7.3 % |
Hardness | 130 HB |
Alclad 2014 T62 aluminum alloy is a high-strength material known for its excellent mechanical properties and corrosion resistance. The Alclad version features a thin layer of pure aluminum on the surface, enhancing its corrosion resistance while retaining the strength of the 2014 T62 core. The T62 temper indicates that the alloy has undergone solution heat treatment, artificial aging, and controlled processing to achieve improved mechanical properties. This makes it ideal for high-performance applications requiring strength and durability.
This alloy is widely used in aerospace, automotive, and military sectors. It is commonly utilized in structural components such as aircraft fuselages, wings, and landing gear, where strength and lightweight properties are critical. The combination of the Alclad layer and the T62 temper makes this alloy suitable for applications in demanding environments, including high-vibration areas and fatigue-prone structures.
In terms of anodizing, Alclad 2014 T62 aluminum alloy benefits from the pure aluminum coating, which facilitates anodizing and improves the alloy's corrosion resistance. However, the high copper content in the core alloy can limit the efficiency of the anodizing process. Regarding weldability, this alloy can be welded effectively with proper techniques, but its copper content increases the risk of cracking. Using specialized filler materials and welding methods can help mitigate these risks and ensure reliable joints.
Bending and forming properties of Alclad 2014 T62 are good, but its high strength requires careful handling during these processes. It is well-suited for use in high-vibration environments due to its excellent fatigue resistance and durability. While the Alclad layer enhances corrosion resistance, the alloy's overall resistance may still be limited by its copper content. Advantages of Alclad 2014 T62 include high strength, good machinability, and improved corrosion resistance, while disadvantages include challenges in welding and limited corrosion resistance compared to other aluminum alloys.
As Alclad sheet; 2014 T62 clad, ASTM B209, ISO AlCu4SiMg, UNS A92014, WNR 3.1255, MIL-A-21180, AIR 9048.080
Choosing Factors for 2014 T62 clad
- Strength: Great
- Machining: Very good
- Weldability: Bad
- Formability: Good
- Corrosion Resistance: Weak
- Heat Treating: Yes
Some Well-Known Applications for 2014 T62 clad
In cooling towers and pipelines,
As parts of military vehicles and in weapons production,
It is generally used in the automotive industry and aerospace industry.
- Sheet