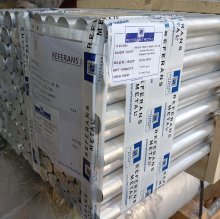
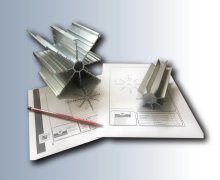
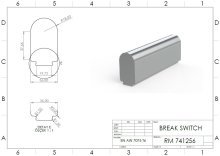
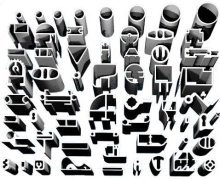
板/板
钣金
棒条/金属板
管道/型材
2219 clad
AMS 4095 / AlCu6Mn / 2219 clad / T351
化学性质 | % 值 |
Silicon (Si) | 0,00 - 0,70 |
Manganese (Mn) | 0,20 - 0,40 |
Magnesium (Mg) | 0,00 - 0,10 |
Copper (Cu) | 5,80 - 6,80 |
Titanium (Ti) | 0,02 - 0,10 |
Iron (Fe) | 0,00 - 0,30 |
Zinc (Zn) | 0,80 - 1,30 |
Aluminium (Al) | Balance |
物理特性 | 值 |
Density | 2.84 g/cm³ |
Melting Point | 543 °C |
Thermal Expansion | 22.5 µm/m-°C |
Modulus of Elasticity | 74 GPa |
Thermal Conductivity | 120 W/m-K |
Electrical Resistivity | 30 % IACS |
机械性能 | 值 |
Proof Strength | 180 MPa |
Yield Strength | 305 MPa |
Shear Strength | 150 MPa |
Elongation A50 mm | %10 |
Hardness | 79 HB |
Alclad 2219 T351 aluminum alloy is known for its high strength, excellent thermal stability, weldability, and enhanced corrosion resistance. The Alclad version includes a thin layer of pure aluminum on the surface, increasing corrosion resistance while maintaining the strength properties of the 2219 T351 core alloy. The T351 temper indicates that the alloy has undergone solution heat treatment, stress-relieving processes, and natural aging, enhancing its mechanical properties. These characteristics make Alclad 2219 T351 ideal for structural components in aerospace, space, and high-performance industrial applications.
In terms of anodizing, Alclad 2219 T351 aluminum alloy is compatible with anodizing processes due to its pure aluminum coating. However, the high copper content in the core alloy can limit the effectiveness of anodizing. Therefore, alternative coating methods are often used to enhance its durability. Its excellent weldability makes it frequently used in applications requiring strong and reliable joints. Proper welding techniques and filler materials help minimize the risk of cracking and maintain structural integrity.
This alloy offers good machinability and formability, though its high strength requires careful handling during bending and forming operations. Alclad 2219 T351 performs exceptionally well in high-vibration environments due to its excellent fatigue resistance and thermal stability. These characteristics make it an ideal choice for components such as aircraft fuselages, space vehicle structures, and other critical parts exposed to dynamic loads and high temperatures.
However, the copper content in the core alloy limits its inherent corrosion resistance compared to other aluminum alloys. While the Alclad coating provides additional protection, supplementary surface treatments may be needed in corrosive environments. The advantages of Alclad 2219 T351 include high strength, excellent weldability, and enhanced corrosion resistance, while its disadvantages include limited inherent corrosion resistance and the need for careful handling during forming. These features make it a preferred material for projects where strength, durability, and thermal performance are critical.
As Alclad sheet; 2219 T351 clad, ASTM B209, UNS A92219, AMS 4095, ISO AlCu6Mn
Choosing Factors for 2219 T351 clad
- Strength: Very good
- Machining: Poor
- Weldability: Great
- Formability: Okay
- Corrosion Resistance: Satisfactory
- Heat Treating: Yes
Some Well-Known Applications for 2219 T351 clad
As a structural element in engineering applications,
In welding requiring high resistance,
It is also used in aircraft fuselages and as booster rockets.
- Sheet