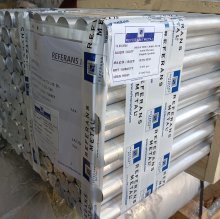
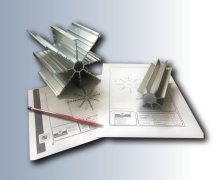

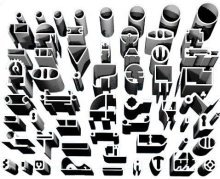
Platten
Blech
Rundstangen
Rohre/ Extrusion/ Profil
5052
AMS 4017 / AlMg2.5 / 5052 / H34
Chemical Properties | % Value |
Silicon (Si) | 0,00 - 0,25 |
Chromium (Cr) | 0,15 - 0,35 |
Manganese (Mn) | 0,00 - 0,10 |
Magnesium (Mg) | 2,20 - 2,80 |
Copper (Cu) | 0,00 - 0,10 |
Iron (Fe) | 0,00 - 0,40 |
Zinc (Zn) | 0,00 - 0,10 |
Aluminium (Al) | Balance |
Physical Properties | Value |
Density | 2.68 g/cm³ |
Melting Point | 607 °C |
Thermal Expansion | 23.8 µm/m.°C |
Modulus of Elasticity | 70 GPa |
Thermal Conductivity | 138 W/m.K |
Electrical Resistivity | 35 % IACS |
Mechanical Properties | Value |
Proof Strength | 214 MPa |
Yield Strength | 260 MPa |
Shear Strength | 145 MPa |
Elongation A50 mm | %11 |
Hardness | 68 HB |
5052 H34 aluminum alloy offers excellent corrosion resistance, good weldability, and medium-to-high strength. Alloyed with magnesium, this material is well-suited for use in harsh environments such as marine and chemical applications. The H34 temper indicates that the alloy has been strain-hardened, stabilized, and partially annealed, providing durability while maintaining good formability and machinability.
5052 H34 is widely used in applications such as fuel tanks, chemical storage tanks, marine equipment, automotive parts, and aircraft structures. It is highly suitable for anodizing, forming a smooth oxide layer that enhances corrosion resistance and provides an aesthetic appearance. Additionally, it can be easily joined using standard welding techniques, maintaining its structural integrity after welding. This makes it a reliable material for structural applications.
In terms of bending and forming, 5052 H34 aluminum alloy is less flexible due to its higher strength, but with proper techniques, it can be successfully formed into complex shapes. It performs exceptionally well in high-vibration environments, offering excellent fatigue resistance and mechanical durability, making it ideal for equipment operating under dynamic loads. These characteristics make it a preferred choice for demanding environments.
The corrosion resistance of 5052 H34 aluminum alloy is one of its standout features. It exhibits excellent durability in corrosive conditions such as seawater, chemical exposure, and humid environments. However, its capacity may be limited in applications requiring extremely high strength. Its advantages include high corrosion resistance, good weldability, and suitability for aesthetic anodizing, while its disadvantages include the need for careful handling during forming and limited strength compared to higher-strength alloys. These features make 5052 H34 an ideal material for projects where lightweight and durability are critical.
Sheets and Plates per; 5052 H34, AMS 4017, AMS QQ-A-250/8, ISO AlMg2.5, WNR 3.3523, UNS A95052, ASTM B209
Cold Drawn Round/Flat Bar and Wires; 5052 H34, ASTM B211, ISO AlMg2.5, WNR 3.3523, UNS A95052, QQ-A-430, AMS QQ-A-225/7
Choosing Factors for 5052 H34
- Strength: Moderate
- Machining: Good
- Weldability: High
- Formability: Decent
- Corrosion Resistance: Very good
- Heat Treating: None
Some Well-Known Applications for 5052 H34
In lighting applications,
As a component of electronic circuits,
It is also used in automobile chassis.
- Tube/Profile
- Plate
- Sheet
- Round/Flat Bar
Mechanical Properties | |||
Thickness (mm) | Proof Strength (Min.) | Yield Strength (Min.) | Elongation A50 mm % |
Over 0.2 up to & incl. 0.5 | 234 | 283 | %3 |
Over 0.5 up to & incl. 1.2 | 234 | 283 | %4 |
Over 1.2 up to & incl. 2.9 | 234 | 283 | %6 |