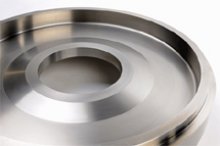
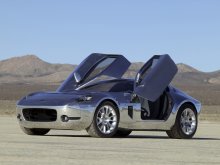
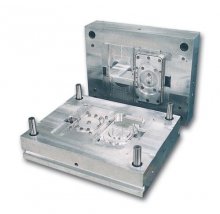
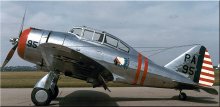
Aleaciones de Aluminio
Click aquí para ver los productos de aleaciones de aluminio
A light, silvery, corrosion-resistant metal with excellent metal-working characteristics - the third most common element, after oxygen and silicium. Aluminum was discovered only at the end of the 19th century, but it now stands beside steel as the most important metal for almost all engineering applications. Aluminum occurs naturally only in the form of compounds.
The basis for the production of the metal is bauxite, a product formed by the weathering of limestone and silicate rocks, which have a high content of Al2O3 (aluminum oxyde) - often in excess of 50%. Pure aluminum is a low-strength material. Significantly higher strength properties – with relatively high tensile and elasticity limits – can be achieved by adding appropriate alloy components. Aluminum alloy materials are classified as “naturally hard” and “heat-treatable” materials.
But, first the question of “why aluminum” needs to be addressed. Alternative materials, particularly a range of steels such as P-20, H13 tool steel, and stainless steels as well as copper-based alloys often containing beryllium, have been employed in tool and mold applications. They offer high strength and wear resistance, and, in the case of the copper alloys, thermal conductivity as well. But no material has all of the desired properties for a given application, and the alternative materials are no exception. They are heavy, often less machinable, and in the case of the steels, have poor thermal conductivity.
Comparison of Aluminum and Steel
Overcoming those deficiencies is where aluminum comes into the picture. Compared to steel, aluminum:
• Has a four-fold increase in thermal conductivity. In molding operations, this reduces the required cooling cycles and also minimizes local hot spots that could lead to part distortion. Aluminum also allows for the design of simpler cooling systems, which require less design and machining time.
• Is lightweight. Aluminum has roughly one-third the density of steel. This makes handling of the tooling and molds easier, and allows faster opening and closing of molds and tools due to reduced inertia. In addition, lighter weight tooling results in less press wear reducing maintenance and downtime. These benefits are particularly relevant to large tools and molds.
• Can be machined and polished more rapidly. Depending on the specific aluminum alloy, machining rates three to ten times faster than that for steel are possible. This reduces the time required for mold production, particularly for large molds with deep cavities.
• Exhibits high electrical conductivity. This, along with a lower melting point as compared to steel, enables the use of electrical discharge machining of aluminum at a rate four to five times higher than for steel.
As a result of these benefits, one aluminum producer estimates that using aluminum for mold applications can save 30% in cost over steel in mold manufacturing, increasing to 40% if the reduced part production cycle times and hence improved productivity are included. One area where steel offers an advantage is in the area of surface hardness. In some applications, such as those involving conventional plastic molding, the base aluminum surface has adequate properties.
However for those cases where higher wear resistance is required, surface treatments of aluminum such as hard anodizing or nickel plating result in aluminum surface hardness levels approaching those of steel. Since there is a range of different conditions under which tool and mold materials must operate, different aluminum alloy and temper combinations have evolved to meet the various needs. Both cast and wrought products are available in a wide range of thicknesses, widths, and lengths.
Each product type has specific characteristics that have been tailored to application needs. Due to its relatively low density aluminum offers perfect cost-saving opportunities in packaging, transportation, production, assembly and maintenance stages.
Aluminum most known applications of aluminum sheets, aluminum profile, aluminum rod, aluminum tube, aluminum round bar, aluminum bar,aluminum plate.
The most well known aluminum alloys as a hard aluminum are 7075 aluminum, 5083 aluminum, 5754 aluminum, 6061 aluminum, 6082 aluminum, 2014 aluminum, 2024 aluminum, 7050 aluminum, 2007 aluminum.
Technical characteristics of aluminum
Relative density
Varies between 2.7 and 2.9 g/cm3, according to the alloy components. This is only 1/3 the weight of steel.
Corrosion resistance
Aluminum forms a natural surface protection layer on context with air. This layer is always reconstituted after removal, providing outstanding resistance to atmospheric corrosion. Pure and very pure aluminum, and also non-copper alloys, are resistant to a very large number of media. For this reason, they are widely used in the construction and chemical industries, the food and beverage industry and for vehicle construction. However the aluminum-based materials with the highest strength ratings – over 500 N/mm2 – have very limited resistance. This has to be compensated by structural design solutions.
Cold and hot forming properties
Aluminum is characterised by a relatively high deformation resistance. Given the use of appropriate technical plants, however, aluminum and its alloys display good to very good cold- or hot-forming properties over a broad spectrum:
• rolling
• extrusion
• forging
• casting.
Good conductor of electricity and heat
Aluminum has a high electricic conductivity (38 to approx. 34 m/Ohm mm² for pure aluminum). The materials used for electrical conductors in practice are mainly pure aluminum and E-AlMgSi materials. The heat conduction level, at approx. 80 to 230 W/m o K is approx. four times that of iron.
Magnetic properties
Aluminum is not magnetic – an important property in the context of electrical engineering, electronics and mechanical engineering.
Surface treatment
A range of surface treatment options are available for aluminum, providing excellent adaptability for virtually any application.
• Anodisation decorative surfaces - wide range of colours surfaces of technical plant and equipment - wear-resistant
• Powder coating in many colour shades - according RAL
• Wet-spray painting in many colour shades - according RAL
• Polishing - mechanical and chemical
• Grinding and brushing etc.
High reflectivity
Aluminum surfaces are naturally good reflectors of light and heat. A number of surface treatments can be applied to adjust the reflectivity and absorption characteristics over a wide range of values.
Jointing techniques
Almost all normal jointing techniques can be used for aluminum and its alloys.
No health hazards
According to current medical knowledge, aluminum is completely free of health hazards.
Recyclability
As used in the industry, the term “recycling” relates specifically to the re-use of scrap and used manufactured products as secondary raw material for the manufacture of new products. Over 1/3 of all aluminum raw materials in use have been produced from appropriate recycling processes, without any loss of quality. Only 5% of the energy required for primary aluminum production is needed for recycling processing. Given the choice between several possible materials, aluminum will often be the most environmentally-friendly and economic option.